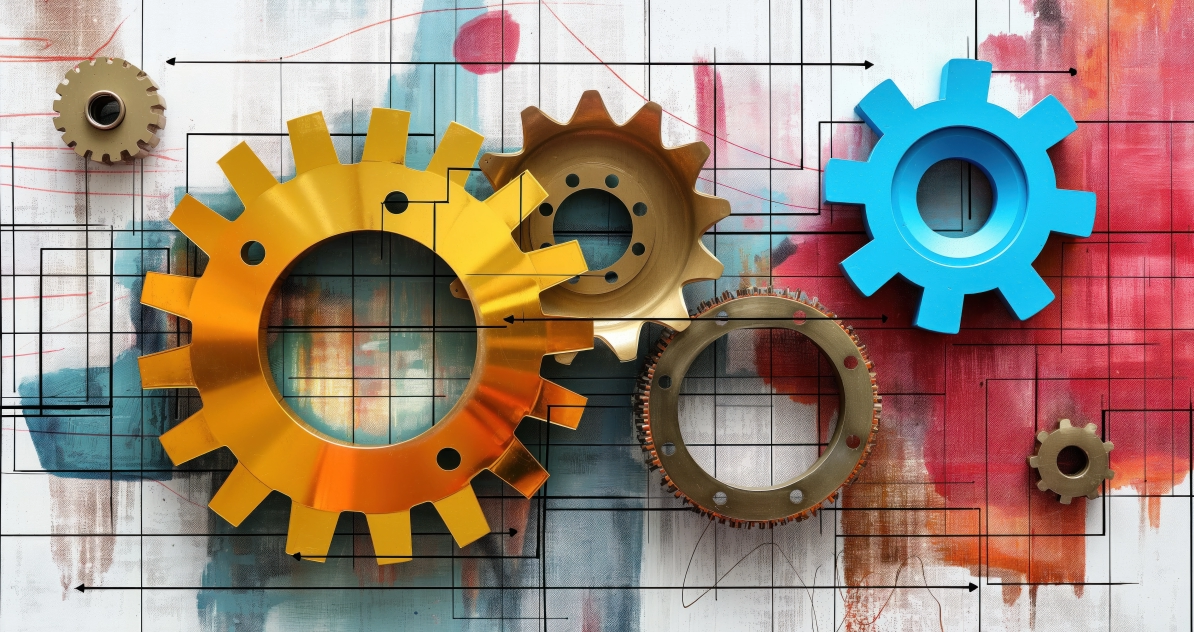
Keep Your Weaving Machinery Running Longer, Smarter, and Stronger
In the competitive world of textile manufacturing, weaving looms are at the heart of production. Whether you operate high-speed rapier looms, airjet machines, or traditional shuttle systems, one thing is clear: well-maintained looms last longer, perform better, and cost less in the long run. Regular, preventive maintenance doesn’t just prevent unexpected breakdowns — it enhances fabric quality, improves energy efficiency, and maximizes the return on your investment. Here are the top maintenance tips every weaving unit should follow to extend the life of its looms and ensure smooth, uninterrupted production.
1. Stick to a Scheduled Maintenance Routine
The most effective maintenance strategy is a planned one. Create a monthly and quarterly maintenance schedule based on the manufacturer’s recommendations. This should include checking mechanical parts, cleaning dust-prone components, inspecting belts and chains, and testing lubrication systems. Logging each service session helps track wear patterns and predict potential issues before they become major repairs.
2. Keep the Loom Clean — Daily
Textile dust, lint, and fiber residue can build up quickly, especially in high-speed looms. This accumulation can clog sensors, block airflow in airjet looms, or cause overheating. A daily cleaning routine, even if just 10–15 minutes per shift, can significantly reduce these risks. Pay attention to reed spaces, tension sensors, nozzles, and electronic compartments.
3. Lubrication is Non-Negotiable
Friction is one of the top causes of component wear in weaving machinery. Always use the correct grade of lubricants specified for your loom type. Over-lubrication can attract dust, while under-lubrication leads to grinding and heat damage. Make sure oiling and greasing points are regularly inspected and maintained.
4. Monitor Air Pressure and Consumption
For airjet looms, compressed air is both a power source and a potential liability. Excessive air pressure can damage parts and increase energy bills, while low pressure causes weft insertion failure. Install gauges and flow meters to monitor usage and detect leaks. Regularly clean the air filter system to ensure efficient performance.
5. Check and Calibrate Electronic Sensors
Modern looms rely heavily on sensors — for weft detection, tension control, lubrication timing, and safety interlocks. These sensors must be calibrated properly and cleaned to avoid false alarms or missed stoppages. A malfunctioning sensor can lead to fabric defects or even loom damage.
6. Train Operators on Machine Handling
No maintenance plan is complete without human involvement. Well-trained operators are your first line of defense against misuse and breakdowns. Ensure your staff understands the correct starting, stopping, and emergency protocols, and encourage them to report unusual noises or performance issues immediately.
7. Use Genuine Spare Parts
When components wear out — and they will — always replace them with OEM (original equipment manufacturer) parts. Cheaper alternatives may look the same but often fall short in durability and precision. Genuine parts maintain the integrity of the machine and preserve its warranty and performance benchmarks.
8. Monitor for Abnormal Vibrations or Noise
Unusual sounds or vibrations are often the earliest indicators of a problem. These could point to loose fasteners, alignment issues, failing bearings, or imbalance in moving parts. Promptly investigate and address such anomalies to prevent bigger mechanical failures.
9. Back Up and Update Loom Software
For looms with digital control panels or smart monitoring systems, always back up machine parameters and update software when new firmware is available. Updates often include bug fixes, improved machine logic, or enhanced compatibility with newer sensors or IoT tools.
10. Maintain a Clean Electrical Environment
Dust and humidity can wreak havoc on a loom’s electrical panels and PLC systems. Ensure control cabinets are sealed, filters are cleaned, and wiring is checked regularly for signs of wear or overheating. A small short circuit can result in a full production halt.