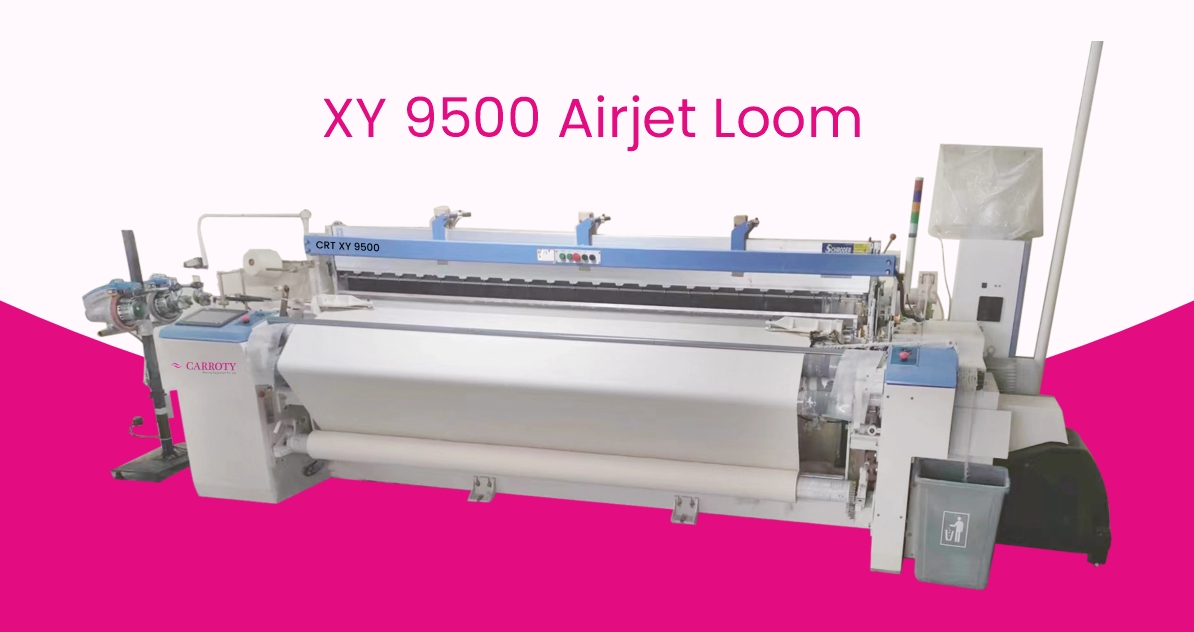
Reimagining Textile Weaving for the Next Generation of Mills
In a textile industry that’s rapidly evolving, manufacturers are constantly seeking a balance between high-speed output and environmental responsibility. The XY 9500 Airjet Loom delivers exactly that — a breakthrough weaving machine that fuses cutting-edge performance with energy-conscious engineering. Designed for the modern mill, this loom isn’t just fast — it’s smart, sustainable, and built to adapt to future production needs.
Let’s take a closer look inside the XY 9500 and explore why it’s quickly becoming the preferred choice for forward-thinking textile operations.
Precision at High Speed
At the core of the XY 9500 is its ability to produce at exceptionally high speeds without sacrificing stability or fabric quality. Engineered for optimized airjet performance, the loom features electronically controlled main and sub-nozzles that ensure accurate and efficient weft insertion. This results in fewer weft breaks, smoother fabric formation, and reduced need for manual intervention — even at speeds exceeding 1100 RPM.
The loom also supports a wide range of fabric types, from lightweight shirting materials to heavier industrial textiles, giving manufacturers the flexibility to diversify their product lines without changing core infrastructure.
Advanced Air Management System
What truly sets the XY 9500 apart is its advanced air consumption control. In most airjet looms, compressed air is one of the largest operating costs. The XY 9500 tackles this challenge with a next-generation air optimization system that minimizes wastage, adjusts pressure in real time, and reduces unnecessary airflow.
Sensors monitor yarn type, pick density, and ambient conditions, making dynamic adjustments to air usage. Over time, this results in significantly lower energy consumption per meter of fabric, contributing to both cost savings and environmental goals.
Designed for Sustainability
Sustainability isn’t an afterthought — it’s embedded in the XY 9500’s design philosophy. From the use of high-efficiency motors to the integration of recyclable components, the machine aligns with global expectations for cleaner, greener manufacturing. The reduced need for compressed air alone can lead to a measurable drop in a mill’s carbon footprint.
Moreover, the loom’s low-maintenance build reduces the frequency of part replacements and unplanned downtimes, helping mills reduce both physical waste and operational disruptions.
Operator-Friendly Interface & Smart Diagnostics
The XY 9500 is designed for the real-world needs of mill operators. A high-resolution touchscreen control panel provides access to intuitive settings, performance data, and alert systems. With built-in smart diagnostics, the machine can detect and display issues in real-time — from weft mispicks to air pressure anomalies — allowing faster troubleshooting and less downtime.
Additionally, connectivity features allow remote access and monitoring, so supervisors can track machine efficiency across the factory floor or even from off-site locations.
Flexible, Future-Ready Investment
With the XY 9500, textile manufacturers gain more than a loom — they gain a production solution that’s ready for long-term adaptability. Whether your mill is producing for fashion, home furnishings, or technical fabrics, the machine’s modular configuration and wide width adaptability make it a future-proof investment.
It also integrates smoothly with Industry 4.0 systems, making it easier for manufacturers to transition toward smart, data-driven textile production.
Final Thoughts
As the textile sector continues to face mounting pressure for faster delivery and cleaner operations, the XY 9500 Airjet Loom emerges as a machine that meets both imperatives. It’s fast, efficient, eco-conscious, and engineered to support the evolving demands of global fabric production.
For textile mills aiming to stay competitive while embracing sustainability, the XY 9500 is more than a machine — it’s a strategy.