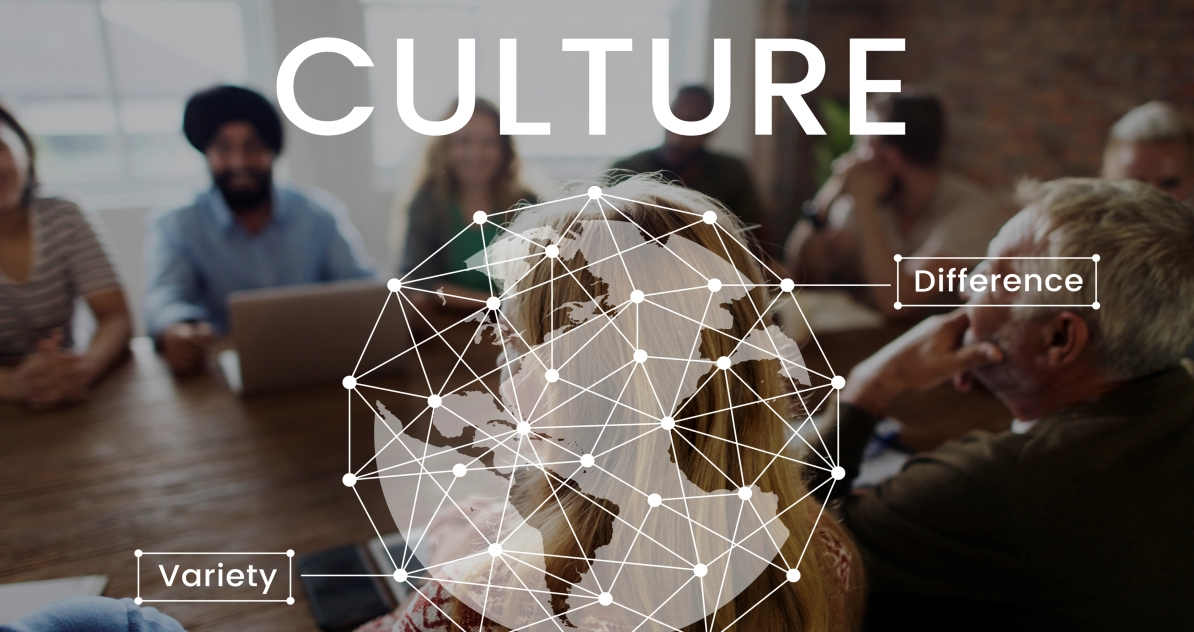
An Industry Perspective on Innovation, Efficiency & Opportunity
The textile weaving industry across Asia is undergoing a significant transformation. Traditionally known as a global hub for mass textile production, the region is now evolving into a powerhouse of innovation, smart manufacturing, and sustainability. As technological disruptions and shifting market expectations reshape global supply chains, Asia’s weaving sector is responding with agility and ambition.
Here are the key trends that are currently shaping the future of textile weaving across Asia:
1. Digitalization & Smart Factories The integration of digital technologies into textile mills is one of the most significant shifts in the industry. From real-time production monitoring to predictive maintenance, weaving operations are becoming increasingly data-driven. Smart looms equipped with touch-screen interfaces, IoT sensors, and centralized control systems are enabling better process visibility, faster decision-making, and reduced downtime. Countries like China, India, and Vietnam are seeing a surge in digital adoption, particularly in export-driven mills.
2. High-Speed Weaving with Energy Efficiency Speed is no longer enough—today, mills are seeking speed with sustainability. Advanced rapier and airjet looms that combine high productivity with low energy consumption are in high demand. Machines that optimize air usage, reduce vibration, and offer efficient yarn handling are becoming essential for competitive and eco-conscious manufacturers. The shift toward such technology is especially visible in markets like Bangladesh, Indonesia, and Pakistan, where power costs and quality expectations are tightly balanced.
3. Focus on Technical Textiles
Beyond traditional apparel and home furnishings, Asian manufacturers are increasingly investing in technical textiles—fabrics used in automotive, medical, filtration, construction, and protective applications. This trend is driving demand for specialized weaving machines capable of handling high-tension yarns, narrow-width fabrics, and complex structures. As government support for technical textiles grows, particularly in India and Southeast Asia, this segment is expected to drive a new wave of capital investment in modern weaving infrastructure.
4. Local Innovation & Machinery Manufacturing
Asia is no longer just a consumer of imported machinery—it’s becoming a developer of world-class weaving technology. Regional manufacturers are engineering machines that rival European models in performance, at a more accessible cost. Companies like Carroty Weaving Equipment Pvt. Ltd., among others, are contributing to this shift by building high-speed rapier, airjet, and jacquard-ready looms tailored for local market conditions. This development is improving access to advanced machinery for mid-sized and growing mills across the region.
5. Sustainable Manufacturing & Compliance
As global buyers increasingly demand sustainable and ethically produced textiles, Asian mills are under pressure to reduce environmental impact. This includes adopting energy-efficient machines, waterless processes, and waste-reducing technologies. Certifications like OEKO-TEX®, GOTS, and ZDHC compliance are becoming prerequisites for global exports. Weaving machinery with a smaller carbon footprint and smart energy monitoring systems is now seen as an investment toward long-term competitiveness.
6. Workforce Upskilling & Automation
While automation is on the rise, the demand for skilled operators and technicians has not diminished. With smarter machines comes the need for smarter handling. Many Asian textile hubs are investing in workforce training programs, either internally or through government-industry partnerships. The aim is to build a new generation of technically skilled workers who can manage, maintain, and optimize advanced weaving machinery.